Recent years have seen a rising trend in power system interruptions caused by electrical cable fires in power system fire accidents around the globe. Therefore, it has become increasingly important to use flame retardant cables in places with a large number of electrical equipment and densely laid cables, such as power plants and substations, to prevent the spread of fires and ensure uninterrupted power supply for important circuits using fire-resistant cables. This need is particularly urgent with the increasing number of high-rise and super-tall buildings, where low-voltage fire-resistant cables can no longer meet the voltage drop requirements of the cables in the fire-fighting circuit. A solution using medium-voltage fire-resistant cables with secondary voltage transformation is urgently needed to meet the power supply needs of the entire fire-fighting circuit.
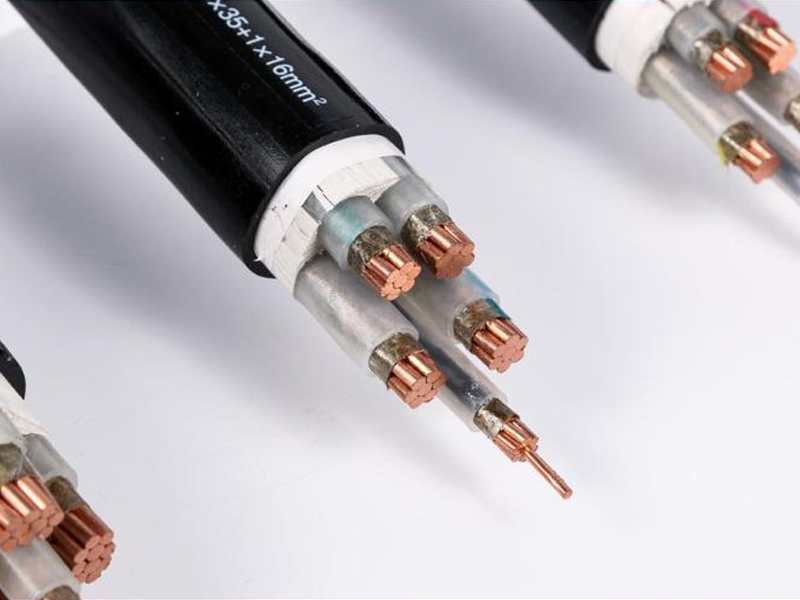
Medium-voltage power cables occupy an important position in power systems, and any fire accident will affect the normal operation of the entire power system. Therefore, the fire resistance requirements for medium-voltage cables continue to increase. The market prospects for fire-resistant cables are very broad and have great market potential.
What is medium voltage fire resistant cable
Medium-voltage fire-resistant cables differ from traditional low-voltage fire-resistant cables. Traditional low-voltage fire-resistant cables use inorganic mica tape wound around the conductor. The inorganic mica tape is composed of mica layers and fiberglass cloth and is a non-combustible material. Even if the external material catches fire in the event of a fire accident, it can ensure that the cable can operate safely and reliably for a certain period of time. However, due to the electrical performance requirements, the scheme of wrapping the conductor with mica tape cannot be used in the design of medium-voltage fire-resistant cables. The wrapping of mica tape causes the surface of the conductor to be uneven, which in turn causes uneven distribution of the electric field inside the cable. At the same time, the wrapped mica tape also causes a large number of air gaps between the conductor layer and the internal shielding, resulting in unqualified local discharge performance of the cable, affecting the long-term service life of the cable, and even causing breakdown of the medium-voltage cable. Therefore, medium-voltage fire-resistant cables need to adopt proprietary structural design to ensure that external heat cannot enter the cable core in the event of an accident. Even in the event of a fire, the insulation effect of the insulation layer can be guaranteed, ensuring that the cable can operate safely and reliably for a certain period of time, winning precious time for fire fighting and rescue.
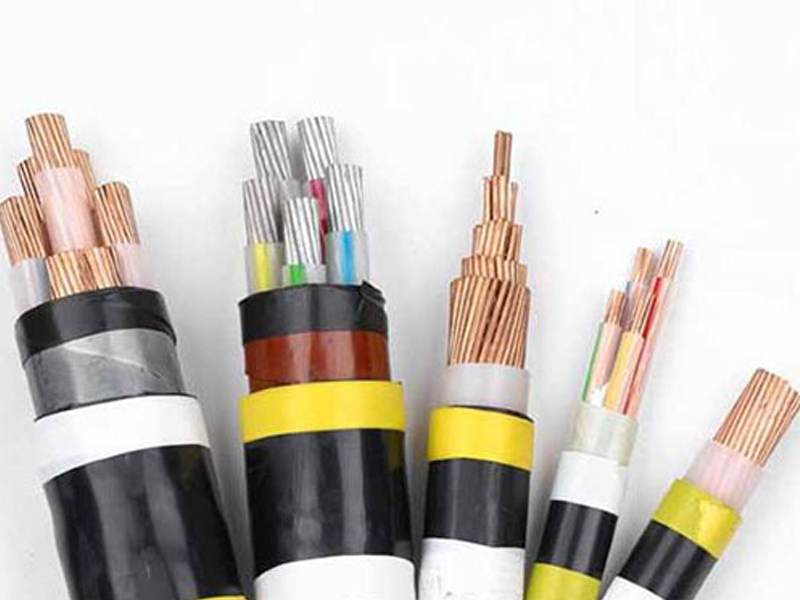
Structural design of medium-voltage fire-resistant cables
- Conductor
The conductor design uses a Class 2 circular compacted copper conductor, which ensures that the cable will not be too hard and will not affect installation and laying. At the same time, the compacting process ensures the smoothness of the conductor surface, which greatly improves the electric field distribution on the surface of the conductor and reduces the possibility of electric field distortion. The surface of the conductor should be smooth, with even pitch, no burrs, no breaks, no oil stains, no oxidation, and especially no burrs on the surface of the conductor. - Triple extrusion
The design of the insulation core uses triple extrusion of conductor shielding, insulation, and insulation shielding. This process ensures the cleanliness of the interface between the insulation and the outside during extrusion, which is conducive to the control of the local discharge index of the cable. In addition, the conductor shielding and insulation shielding should use semiconductive materials. Although the conductor uses compacted conductors, it is still not very smooth. Therefore, extruding semiconductive materials can ensure that they are equipotential with the conductor, further equalizing the distribution of the electric field. The nominal thickness of the insulation should comply with national standards, and the average thickness of the insulation should not be less than the nominal value. The thinnest part of the insulation should not be less than 90% of the nominal thickness - 0.1mm. In order to facilitate construction, the insulation shielding should use peelable semiconductive shielding material. The surface of the insulation core should be flat and smooth, without any defects such as scorching or abrasion. - Metal shielding
A 0.1mm nominal thickness copper tape shield is used for metal shielding. The design of the copper tape layer should fully consider the conductivity performance to ensure that the cable can effectively transmit short-circuit current in the event of a fault. - Cable filling
The cable core uses flame-retardant filling, and the filling material should not be easy to absorb moisture and should be suitable for the operating temperature of the cable. - Fire-resistant layer
The fire-resistant layer design uses ceramic fire-resistant materials. It can crust and ceramicize at high temperatures during combustion, avoiding the diffusion of combustion heat to the cable core, effectively protecting the insulation from thermal deformation at high temperatures. The nominal thickness of the fire-resistant layer should comply with the requirements of the product structure table, and the thinnest part should not be less than 80% of the nominal thickness - 0.2mm. In conjunction with the high flame-retardant oxygen barrier layer, it achieves an equivalent effect of fire resistance. - Sheath
The sheath design uses low-smoke and halogen-free flame-retardant polyolefin materials. The material produces extremely low smoke and does not produce harmful gases during combustion, avoiding secondary harm to personnel. The nominal thickness of the outer sheath should comply with the design requirements of the product, and the thinnest part should not be less than 85% of the nominal thickness - 0.1mm. The outer sheath should be tightly wrapped on the insulation layer, with a smooth surface, no air holes, cracks, impurities, or mechanical damage, and the cross-section should have no visible air holes or sand eyes. Water ingress during extrusion should be strictly prevented. The surface of the outer sheath should be printed with continuous markings such as the manufacturer's name, product model, voltage level, and specifications.
Electrical properties of medium voltage fire-resistant cables
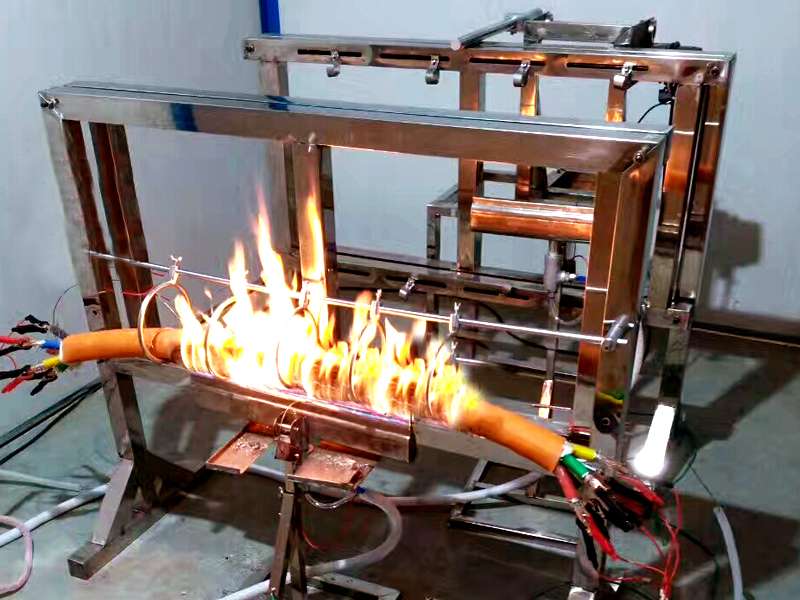
AC voltage test:The test voltage frequency is (49~61) Hz AC source, the detection method complies with the GB/T 3048.8-2007 regulations, and a 3.5U0/5min AC voltage is applied between the conductor and the copper tape shield of each phase. The cable does not break down.
Conductor DC resistance: The double-arm bridge is used to measure the DC resistance of the conductor, and the detection method complies with the GB/T 3048.3-2007 regulations. The DC resistance of the conductor at 20℃ should not exceed the standard specified value. Partial discharge detection: The detection method conforms to the GB/T 3048.12-2007 regulations, and the test sensitivity is 5pC or better. Under the condition of 1.73U0, there should be no detectable discharges produced by the tested cable.
Fire resistance of the cable
Test according to the test method in Appendix B of TICW 8:
- The sample is not broken down when the rated cable voltage U0 is applied to the entire test duration (any false breakdown phenomena, such as terminal face flashover discharge, should be eliminated, and the test should continue until the specified time);
- Within 1 hour after the test is completed, check the integrity of the sample. Under the condition of maintaining the original state of the test, apply a test voltage of 3.5U0 for 15 minutes without breakdown (any false breakdown phenomena, such as terminal face flashover discharge or internal discharge, should be eliminated).
Conclusion
Medium-voltage fire-resistant cables play an immeasurable role in reducing property losses and guaranteeing personnel safety in fire accidents. In power distribution networks or industrial systems, medium-voltage fire-resistant cables will surely be widely used.