Metal conductors are an important part of wire and cable products. Copper and aluminum, as the basic materials of wire and cable conductors, have been widely used in the power industry all over the world. Conductor materials should not only meet the application requirements in terms of performance, but also reduce product costs, so as to conform to the background of the era of comprehensive utilization of resources, energy conservation and environmental protection.
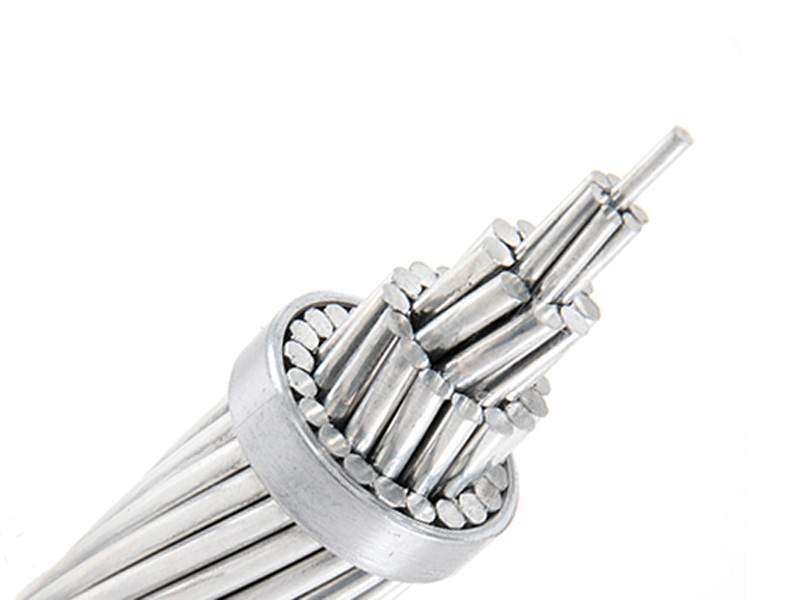
Development of All Aluminum Alloy Conductor(AAAC)
As early as the 1830s, civil construction in the United States and Canada began to use pure aluminum conductors in power cables. Due to the lack of physical, mechanical and electrical properties of pure aluminum, and the installation and laying process at that time was not yet Imperfect, accidents often occurred in application. After World War II, U.S. cable companies, U.S. Underwriters Laboratories and related research institutions began to devote themselves to the development of all-aluminum alloy conductors.
In 1968, the first cable with 8000-series aluminum alloy as the conductor was successfully developed, and then began to be promoted in the United States, Canada and other countries. It is mainly used in military bases, residences, public buildings and wind farms, and its production has been standardized.
What is AAAC?
The all-aluminum alloy conductor is a new type of energy-saving product. It is a high elongation aluminum alloy material, which is made by adding copper, iron, magnesium and other elemental materials into pure aluminum, and through compression stranding technology and metal annealing treatment to tighten the existing voids in alloyed aluminum. The all-aluminum alloy conductor makes up for the shortcomings of the previous pure aluminum cables. Its insulation material uses flame-retardant silane cross-linked polyethylene, and the outer layer adopts metal chain armor structure, so the gap between the conductive performance of the all-aluminum alloy conductor and the copper core cable is greatly reduced, but the creep resistance, bending performance and corrosion resistance are greatly improved, which ensures that when the cable encounters overload and overheat during use, stability can be maintained for continuous performance.
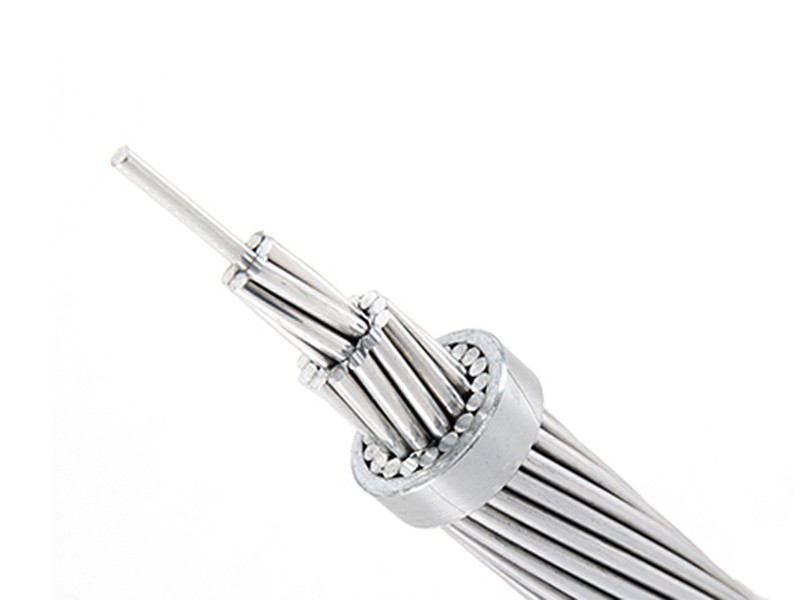
In the production process of the all-aluminum alloy conductor, advanced compaction technology can make the filling coefficient of the conductor reach 93%; and the all-aluminum alloy conductor is made of silane cross-linked polyethylene, this insulation only needs PVC 2/3 of the thickness can far exceed the conventional insulation performance. However, the filling coefficient of copper can only reach 80% in general, and the commonly used insulation is polyvinyl chloride, so the outer diameter of the all-aluminum alloy conductor can be the same as that of the copper core cable by only increasing by 11% on the basis of the copper core cable. It can be seen that all-aluminum alloy conductors can be used normally without changing the original pipeline design of copper core cables.
Why use all-aluminum alloy conductors?
All aluminum alloy conductors can completely replace copper core cables in terms of performance, and all aluminum alloy conductors can basically be used where copper core cables can be used. Compared with copper core cables, under the premise of consistent electrical performance, the conductors of all aluminum alloy conductors can resist creep, with the characteristics of high flexibility, strong ductility, low rebound, and stable connection. Its insulation has the characteristics of high temperature resistance, anti-combustion, anti-aging, strong durability, low-carbon and environmental protection. Its armor layer is made of aluminum alloy with interlocking armor, which has a self-locking form. Strong and tough armor layer ensures that the cable can withstand strong destructive forces from the outside world. Its outer sheath is made of lead-free and cadmium-free PVC material, which can be installed under humid environmental conditions or directly buried in cement. In general, the all-aluminum alloy conductor has better bending performance, ductility and creep resistance performance basically the same as that of copper core cable, light weight, energy saving and environmental protection, etc., which reduces the wear and tear between equipment and cables, making Installation work is easier. Under the premise of providing the same electrical performance, the weight of the all-aluminum alloy conductor is half of the copper core cable. Its cross-section is 1.3 times bigger than the traditional copper core cable, and the price is 40% lower than the traditional copper core cable. The comprehensive cost performance advantage is huge.
5 properties of all aluminum alloy conductors
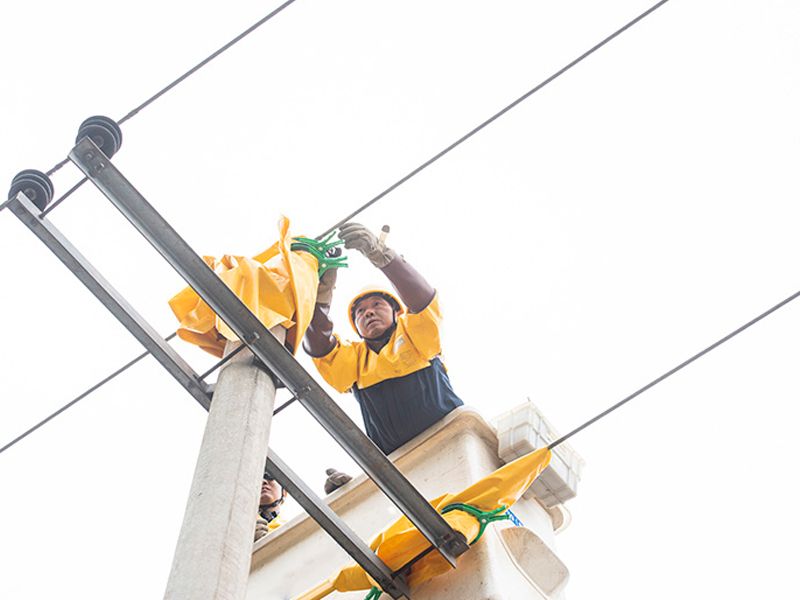
Conductivity
- Realization of ampacity
When the cross-sectional area of the all-aluminum alloy conductor is 1.3 times bigger than copper conductor, its electrical properties are the same, that is, the same ampacity, electric resistance and voltage loss as copper are realized. - Loss of the line
The aluminum alloy belt interlocking mosaic material is a non-magnetic material, even if there is a three-phase unbalanced current, it will not generate eddy currents, which can reduce the loss of the line.
Anti-corrosion properties
When the surface of aluminum is in contact with air, a thin and strong oxide layer is formed. The surface of this oxide layer is very resistant to various forms of corrosion, forming the anti-corrosion properties of aluminum itself. Rare earth elements further improve their corrosion resistance, especially in electrochemical corrosion performance. In some sulfur-containing environments, such as in some places such as railway tunnels, the corrosion resistance of aluminum alloys has more obvious advantages than copper.
Mechanical performance
- High extension
Elongation is an important indicator of the mechanical properties of conductors, and an important symbol that relates to the quality of products and the ability to withstand external forces. The elongation of the all-aluminum alloy conductor after annealing can reach 30%, while the elongation of the copper cable is 25%, (the elongation of the ordinary aluminum rod is 1.5%), which is a important indicator that the all-aluminum alloy conductor can replace the aluminum core cable and copper core cable. - Strong flexibility
Due to its unique alloy formula and processing technology, the all-aluminum alloy conductor makes the flexibility 30% higher than the copper cable, so there will be no cracks, and fewer safety hazards during installation. - Easy bending
The bending radius of the copper core cable is 15 to 20 times larger than its cable diameter, while the bending radius of the all-aluminum alloy conductor is only 7 times the smallest relative to its cable diameter. So using the all-aluminum alloy conductor to perform terminal connection is easier, which greatly reduces the space for installation layout and makes it easier to lay cables. Thus installation costs is reduced effectively. - Low rebound
At room temperature, the copper core cable and the all-aluminum alloy conductor are bent at 90 degrees respectively. After the stress is released, the rebound angle of the all-aluminum alloy conductor is 60% smaller the copper core cable. Because the all-aluminum alloy conductor has no memory, the rebound performance is better than the copper core cable. During the installation process, it is more beneficial to the tightness of the terminal connection joint, and it is easier to compress, which improves the stability of the connection.
Connection performance
When the all-aluminum alloy conductor is annealed, some elements added to it produce high-strength creep resistance, which greatly improves its connection performance. Especially the key is that even when the current is overheated and overloaded, the possibility of creep of the all-aluminum alloy conductor is very small, which ensures the stability of their connection. So the electrical connection of all aluminum alloy conductors and copper core cables is equally reliable in stability.
Economic performance
Under the premise of the same electrical performance between the all-aluminum alloy conductor and the copper core cable, the cost price of the all-aluminum alloy conductor is about 13% to 20% lower than the copper core cable, and there is also a saving in installation costs. Due to the high bending performance and lighter weight of the all-aluminum alloy conductor, especially the installation of aluminum alloy belt interlocking armored cable does not require bridges and pipes, saving a lot of steel, and the installation cost can be reduced by about 20%.
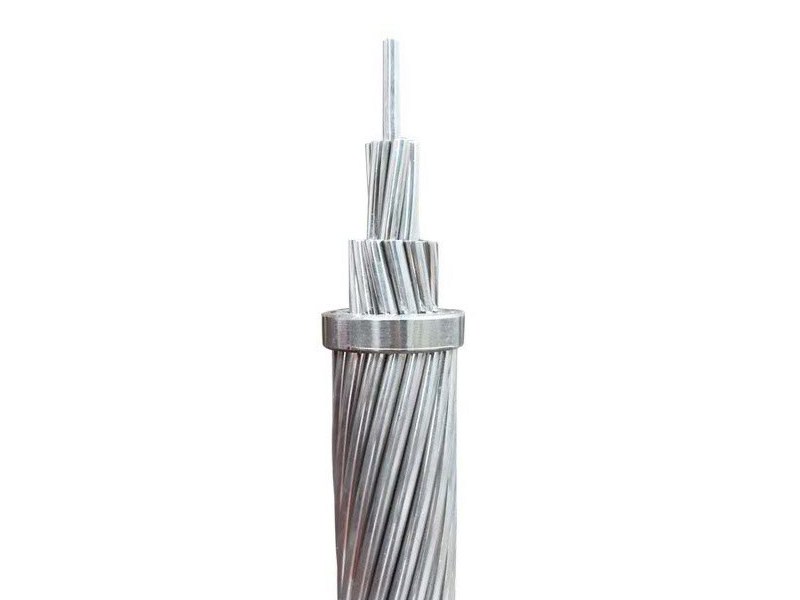
Some disadvantages of all aluminum alloy conductors compared with copper core cables
1. Since the resistivity of the all-aluminum alloy conductor is lower than the copper conductor, the same electrical function can only be achieved if the cross-section is larger than the copper cable. So the outer diameter of the finished product is 10% to 20% larger than the copper cable. This is the main disadvantage of all aluminum alloy conductors. But whether the link of the equipment or the layout of the cable, this size difference is within the allowable range of the design of the pipe.
2. The scope of application has certain limitations. In the special application environment with high temperature resistance above 700 ℃, the all-aluminum alloy conductor should not replace the copper core cable.
3.The production process of all-aluminum alloy conductors is different from traditional copper core cables. The production process and auxiliary materials cost are relatively high, and the core of its quality assurance is still in the conductors. Therefore, the process of manufacturing all-aluminum alloy conductors still needs to be improved.
Epilogue
The good mechanical properties and conductive properties of aluminum alloy power cables make it widely used in various fields of the national economy, such as high-rise buildings, subways, airports, tunnels, underground buildings, etc., and can also be used in metallurgy, coal mines, Shipbuilding, nuclear power plants, aerospace, military and other industries, as well as automobiles, public transportation facilities, etc., have very promising market prospects and attractive prospects, and will surely become the mainstream of power cable development in the future.